Product audit is one of the quality management tools that helps organizations maintain a high standard of manufactured parts. Proper implementation of this activities increases customer confidence by minimizing the risk of quality problems.
Product audit: definition
This type of audit is defined as the process of independently assessing and analyzing a product to verify whether it meets certain standards, specifications, and customer expectations. During a product audit, organizations typically establish specific evaluation criteria. These criteria may include the following aspects:
– technical parameters
– compliance with requirements
– product safety
– durability
– aesthetics
The product audit is also valuable for identifying areas for continuous improvement in production processes.
Product audit – frequency
Many customers in the automotive industry do not have specific requirements regarding the frequency of product audits. Most often, when analyzing customer documentation, we can come across the statement that they should plan them in a given calendar year.
How to approach the issue of frequency? One reasonable strategy is to consider the volume of parts delivered to the customer. If in our portfolio we produce the most products for the VW customer, fewer for Ford, and the least for Stellantis, then most audits should be carried out for the first OEM.
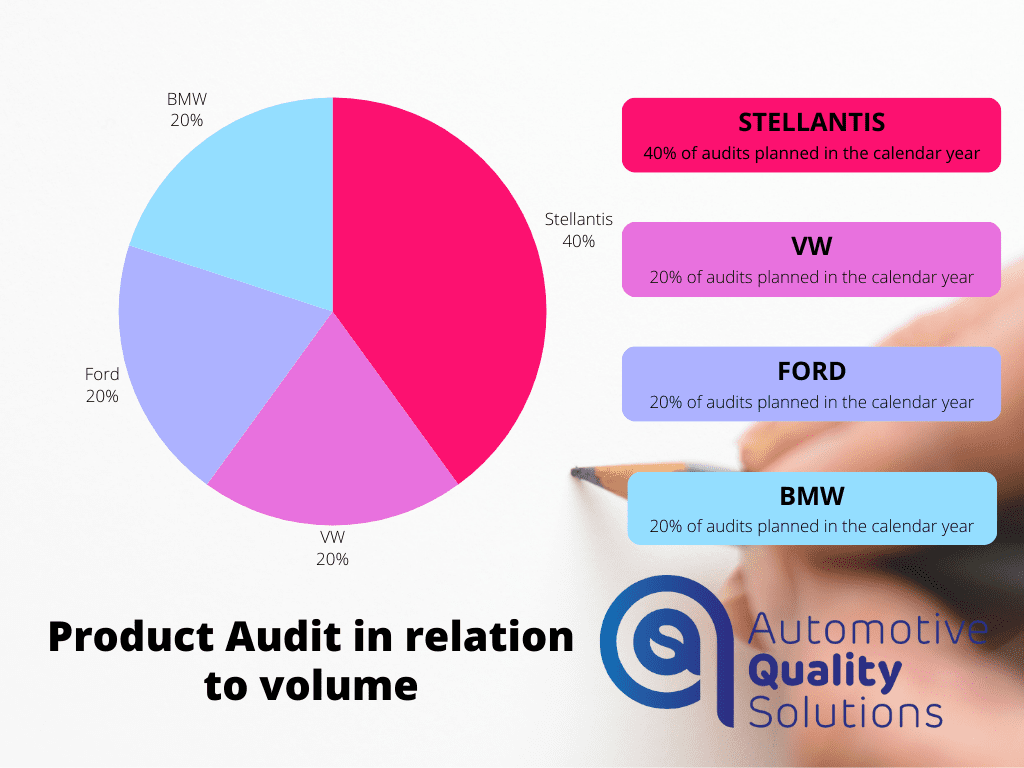
The same applies to the audit methodology. The exception are German manufacturers who refer to the VDA 6.5 manual. More information on this topic can be found in a separate article.
A Product Audit is not a Requalification
An activity very similar to the verification of a finished product is product requalification (IATF 8.6.2) – separate article related to this topic can be found here. Even though at first glance it seems almost the same – because it concerns a finished product – it is worth separating it. Why?
– a product audit is a kind of validation relating to tests and controls. We define them during the production process.
– requalification aims to re-perform the scope of validation tests that the organization previously carried out during the pre-launch phase.
Of course, we will be able to have common elements in both activities (such as carrying out measurements). However, we should mark them as two different activities in the Control Plan.
Another common feature is that in both cases we do not need to test for every drawing number. If we produce very similar products (e.g. fuel lines or seats with different trim colors), we can agree with the customer to carry out tests for a specific representative of the product family. This is one of the basic optimization strategies.
But how to define such a representative of a product family? The best solution is to choose the most comprehensive part that we produce. Thanks to this, we gain an additional argument in a discussion with the client when defining the scope of revalidation tests.
What to remember during implementation and management?
If you are conducting a product audit in the organization you currently work for, it is worth keeping the following issues in mind:
Reporting nonconforming results and management’s response
If the audit result is negative, the organization should immediately take appropriate corrective action on the blocked production batch. In my career, I have had a situation where a quality manager, knowing that the results were negative, did not take any action. Ultimately, we shipped the products to the customer anyway.
As you can see, even if management does not support our efforts, all our work may go to waste.
VDA 6.5 requirements and other customers
If, in addition to cooperation with German customers (e.g. VW), you supply products to other manufacturers, it is worth extending the VDA 6.5 methodology to other customers. Thanks to this, during the Certification Body IATF audit, we will not have to prove to the auditor that the controller who worked on the second shift had the appropriate authorization to conduct audits for VW, and the controller from the third shift is dedicated only to verifying the Ford customer’s production – and does not have to have VDA 6.5 qualifications.
More about sampling frequency and size
Based on both issues, we should define:
– functional characteristics,
– production process stability, which is important in the initial phase of project launch,
– classification of characteristics in PFMEA
To sum up, a product audit is an important tool of the quality management system. Measurably helping organizations maintain the high standard of their products while increasing customer trust.
Dariusz Kowalczyk