One of the most critical aspects in the realm of production processes is customer satisfaction. With increasing market demands, safety regulations, legal requirements, environmental standards, and the widespread use of modern technology, manufactured products are becoming progressively more complex.
To meet these evolving requirements, manufacturers and suppliers must diligently ensure that their products comply with customer specifications at various stages of the production and supply chain. One of the tools utilized for such verification is the Product Audit according to the VDA 6.5 manual.
What exactly is a Product Audit? It involves the thorough examination of product compliance with specified requirements. The scope of these requirements may vary based on the type of client. Primarily, there are two categories: external customers, who are outside our company, and internal clients, situated within our facility. Internal clients may include:
- The subsequent production operation within the process,
- Another department within the production process, or
- A quality checkpoint typically positioned at the end of a specific production stage.
The Product Audit according to VDA 6.5 encompasses several key stages
1. Audit Planning
The initial step in conducting a product audit according to VDA 6.5 is meticulous planning of the entire process. During this phase, the team defines the audit objectives, scope, location, necessary infrastructure/tools, and schedule.
Planning stands as a pivotal element in ensuring an effective and efficient audit. The unit organizing the Product Audit should establish, at minimum:
- The products slated for audit,
- An assessment of the characteristics/features of the product,
- The ranges defining compliance and/or non-compliance with the guidelines for each characteristic,
- The tools required for measuring selected features,
- The calibration schedule for these tools,
- A matrix outlining qualified employees responsible for conducting the Product Audit,
- Monitoring protocols for the entire audit process,
- Contingency plans for potential corrections and adjustments.
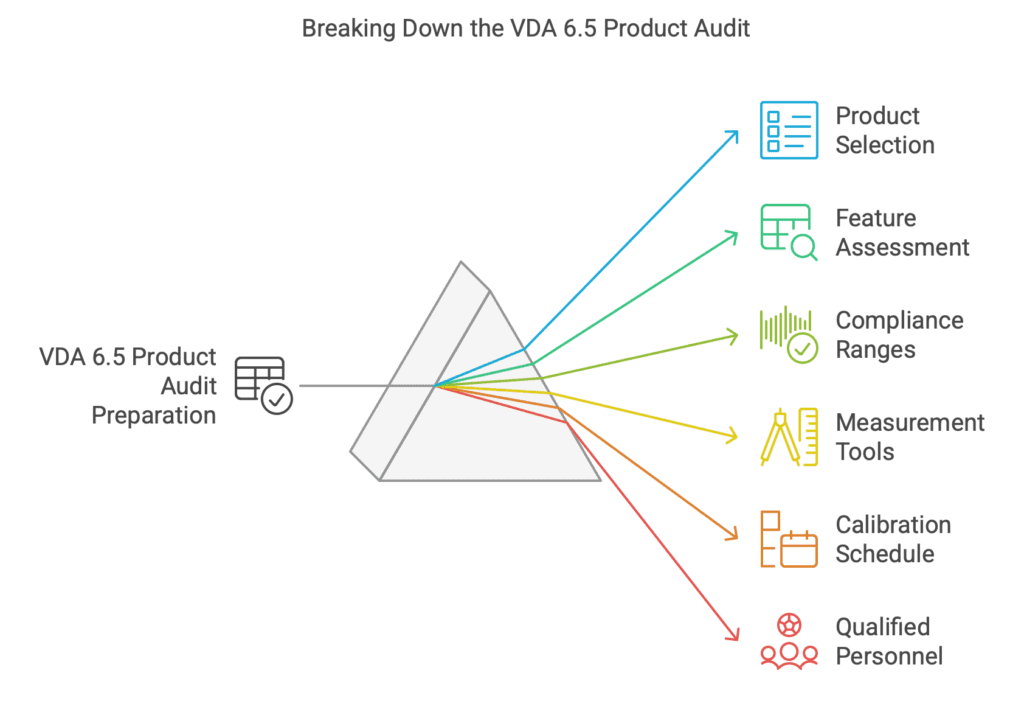
2. Audit Preparation according to VDA 6.5
Preparing for the audit entails a thorough examination of documentation and the identification of critical areas. During this phase, the audit team prepares to evaluate the compliance of production processes with quality requirements. Examples of characteristics that will undergo assessment may include:
- Dimensions
- Functionality
- Appearance
- Material compatibility
- Corrosion resistance
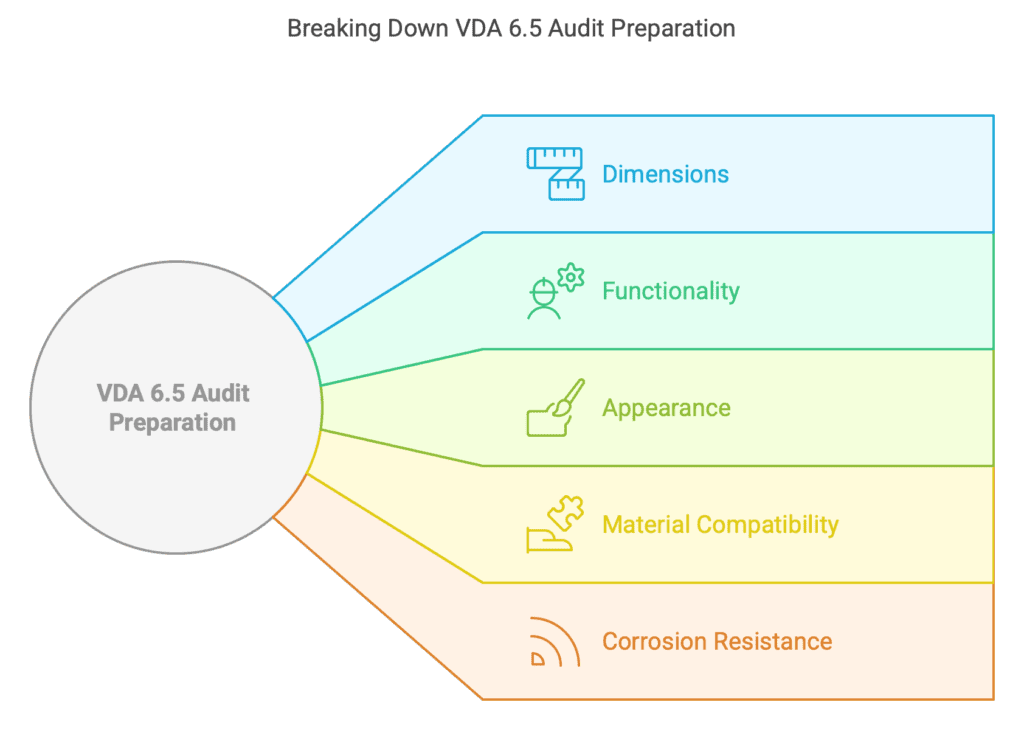
3. Audit conducting according to VDA 6.5
During the audit itself, a qualified audit team utilizes established criteria to assess the compliance of parts against the requirements. At this stage, a checklist comprising parameters to be assessed proves valuable. Each sub-point, upon completion, should be properly marked.
Additionally, other technical documentation, such as technical drawings and dimensional reports, along with reports from previous audits, can aid in the assessment process. Following the steps outlined below is standard practice at this stage:
Part selection for audit
Ideally, the selection of parts for the audit should be random, initiated by the auditor conducting the activity. The auditor selects a part (a specific type of product from the production batch) and informs the process owner about it to ensure awareness and completion of the production process.
The audit team must ensure that the product owner remains unaware of which part will be selected for audit during the production process. This ensures that the production process of the chosen part proceeds serially, without any additional adjustments that the process owner might be tempted to make to improve the part’s evaluation in the audit.
Handling and marking of parts
First of all, carefully transport the parts to the audit site to prevent any changes in their properties or parameters during handling. Furthermore, each part should receive appropriate marking to inform other users about its purpose.
Conducting the assessment
During the audit, the qualified team evaluates the part against the established criteria.
Results documentation
It is crucial to precisely describe the results of the audit. It is good practice to also prepare photographic documentation of any potential discrepancies observed.
Return of the part to the production process
Parts can be returned to the production process if no parameters of the part have changed since it was initially transferred from the production process. According to the guidelines outlined in the company’s standards of conduct, defective parts should be moved to a separate process, primarily referring to the handling of non-conforming parts.
4. VDA 6.5 Audit Report
An integral part of the entire Product Audit is the Audit Report. We should prepare the report in a clear manner that effectively shows and describes any resulting discrepancies. The department responsible for non-conformities should be able to identify the location on the part where the failure is located and the type of error based on the report.
According to VDA Guideline 6.5, we categorize faults according to their severity, with examples divided into 3 categories: A, B, C.
5. Implementation and verification of countermeasures
After presenting the Audit report containing the list of non-compliances, responsible areas are required to present and implement corrective actions. It is necessary to analyze the root causes of the error at this stage. Tools such as the Ishikawa diagram or the 5 Whys method can be helpful.
Once the cause is identified, appropriate countermeasures can be developed and implemented. We can mainly divide countermeasures into two types: immediate and long-term.
Long-term actions
The optimal solution involves implementing changes that do not incur additional costs with each subsequent production and are permanent. For example, this could include altering the geometry of a part sourced from a sub-supplier or making a one-time adjustment to the production equipment to eliminate the issue.
We refer to these actions as long-term countermeasures. However, implementing long-term actions often takes time, and to ensure that the company remains profitable, production must continue. In such situations, we implement temporary actions.
Interim/Immediate actions
To avoid disruptions in production while addressing issues identified during the Audit, we implement temporary containment actions. For instance, this might involve adding an employee to the production line to prevent a problem from occurring.
However, we typically implement such solutions, resulting in additional costs for each subsequent production, only until we establish long-term actions.
The team should revisit and evaluate the Product Audit according to VDA 6.5 in the next phase after implementing each action to assess the effectiveness of the corrective measures.
Rafal Golembowski
Bibliography:
1. VDA 6.5 Product Audit (3rd edition. March 2020)