QRQC training agenda:
1. Quality Management System:
- Risk identification methods in the process
- Lean Management – identification of continuous improvement tools
2. QRQC – building a production management team
- Quick Response Quality Control – a method of quick response to failures
- specificity of tasks and responsibilities in the team
- team organization, communication, reporting, escalation
3. Quality problems solving on the production line:
- QR – quick response to errors: discussion of actions to be taken in the case of e.g. complaints, changes in the process or event (immediate actions – 24h) together with the definition of responsibility and verification of implemented actions and their effectiveness
- 3R – San Gen Shugi, PDCA cycle together with explanation of methods with practical examples of use in the production area.
- GEMBA β go to place where issue has been signalized
- GENBUTSU – part analysis
- GENJITSU – working with data
- Involvement of QRQC teams to perform analysis directly on the production line – eliminating the belief that we know the production area without verification at the place of occurrence
- Red box – this is not only a physical place where we place parts out of specification in the process, but also support for QRQC teams, which can be given by managers.
- Presenting how to manage issues with expired deadlines
- AQM β auto-quality matrix
Tool for QRQC teams, based on which we are able to analyze not only the causes of problems but also assess the level of detection and response to errors in the process.
- AQM presenting as a method that can be used in situations of increased employee turnover, Quality Wall kick-off and in a situation where the company is analyzing the possibility of control frequency reducing (elimination of MUDA)
- On job training (OJT):
- Team work observing method at each level of the organization. It allows the supervisor to work directly with the team to improve work efficiency, analyzes quality and to eliminate recurrence (a problem that occurred).
- Presentation of the form, methods of performing OJT
4. Problem solving β FTA PDCA
- QR – problem identification (5W2H)
- Immediate response actions
- Sorting organization and conclusions
- Assignment task – process speeding up
- FTA analysis – potential cause of the error identification
- FTA analysis – potential reason for not error detecting
- 5Whys – root cause identification
- Defect reproduction
- Corrective actions approval
- Activities effectiveness verification
5. Lesson Learned Card β analysis results
- Learning from mistakes
- Activities standardization
Submit a request
Automotive Quality Solutions
Training program
PDF file
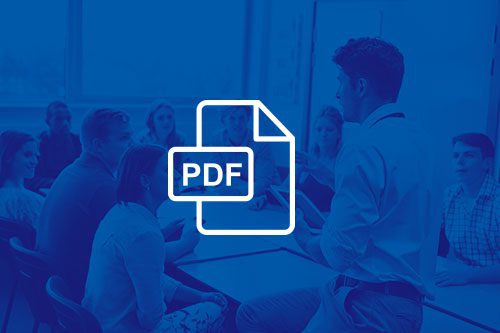
Automotive Quality Solutions
Participant will learn:
- what are responsibilities in QRQC team
- how to report and escalate as part of QRQC (from LINE to PLANT QRQC)
- how and when to define actions for signalized issues
- what are the methods and tools to identify the root cause
- how to verify, if the implemented actions are effective
- how to find out beneficial to eliminate the root cause and not the effects of its occurrence
- how QRQC offers the possibility of continuous improvement
- skill that gives you the opportunity to perform and supervise analyzes
- how standardization process improves company’s results
Automotive Quality Solutions
Duration:
- 2 days (each 7 hours)
Price:
For internal training sessions, please contact our office directly.
Price includes:
-
Participation in the training
-
Training materials
-
Certificate of completion