Stellantis-FCA CSR training agenda:
Training performed according to revision nr. 5 of Stellantis-FCA CSR published at 15 March 2021.
1) Connection Between IATF Requirements and Customer Specific Requirements
2) Stellantis-FCA CSR (EMEA/LATAM) Aligned with IATF:
-
Quality Requirements for Suppliers (QRS) PRO-00109 β a new harmonized requirement developed in cooperation with Stellantis (formerly FGP.42) and the Statement of Requirements
-
Basic Requirements Checklist (BRCL)
-
Additional Quality Requirements (AQR)
-
Forever Requirements (FR) β SQ.00012
-
Manufacturing Feasibility Assessment (MFA)
-
Supplier Quality Management System development and oversight
-
Escalation criteria
-
Layered Process Audits (LPA)
3) Qualification of Externally Purchased Production Parts β Procedure 07740:
-
PE β Plant Evaluation (formerly Benestare) β sample ordering process, handling of negative results, and introduction to PRO.00106 (PPAP Approval)
-
SPV β Supplier Product Validation (formerly AQF) β creation, approval, definition of requalification tests, and introduction to DVP&R β Design Verification Plan and Report (Stellantis Harmonized, QR.10022)
-
EPV β Engineering Product Validation (formerly PI) β sample submission and result verification
4) Procedure 08090 β Interim Approval Authorization (IAA):
-
Theory and practice
5) SQ.00010 β Advanced Quality Planning & Production Part Approval Process
-
Replaces ex-FGP13 and FGP14
6) GSQN.007 β Capacity Assessment Procedure
-
Formerly PDR (SQ.00008)
7) Procedure 9.01102 β Supply Quality
8) Procedure 9.01103 β CQC
9) GSQN.0004 β Proactive Containment Procedure (formerly SQ.00009 SLP)
10) FGP 16 β 3CPR (formerly Control Shipment Level) & New Business Hold
11) Procedure 9.01120 β Report Characteristics
12) Supplier Quality Monitoring & Global Stellantis Supplier Claim Management (GSQN-001):
-
Procedure 08018 β Quality monitoring for directed materials
-
Claims classification
-
Bid list rules
-
Practical guidance on 8D reports and Cross-Out Requests
13) Practical Information:
-
Codesign β what it is and its importance in collaboration with Stellantis (formerly FCA)
-
Supplier Code β how it relates to alphanumeric codes
-
Practical notes on cooperation with Stellantis plants in Europe, Brazil, and India
-
Best practices for resident engineers in Europe and India
Submit a request
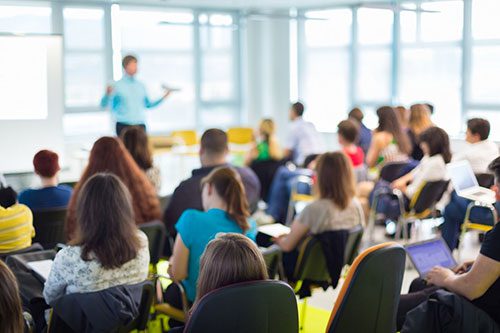
Training program
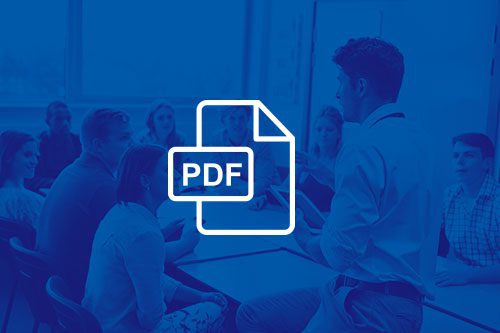
Automotive Quality Solutions
Thanks to Stellantis-FCA CSR training, participant will learn:
- Correct interpretation of Stellantis xFCA requirements with respect to IATF
- Which Stellantis xFCA standards are not actual compering to published IATF
- Understand the standards in force in cooperation between customer and supplier
- Get practical insights in cooperation with customer locations located in Europe
- Best Practice for residents of European plants
- What are the differences between theory and practice for the Interim Approval Authorization IAA
- Which launch phases are present in the Stellantis xFCA terminology and what must be completed in the individual commissioning phase on the vendor and customer side.
- Codesign – what it is and why it is so important to work with Stellantis xFCA
- Supplier codes – Alphanumeric code matching for customer locations located in different countries.
Automotive Quality Solutions
Benefits for the company:
-
Understanding the Plant Evaluation (PE) process (formerly Benestare) β a positive evaluation can accelerate reimbursement of supplier investments in customer-owned equipment
-
By participating in the Stellantis xFCA CSR training, you will improve response times when reporting quality issues at customer sites by learning from the experience of resident engineers with strong relationships with customer quality departments
-
Learn what is essential when submitting a Non-Conformity Ticket (NCT) or a Partial Cross-Out Request
-
Strengthen long-term relationships with both Stellantis SQEs and customer quality departments through practical knowledge of Stellantis-specific requirements
Automotive Quality Solutions
Duration:
2 days (eachΒ 7,5 hours)
Date of Open Training:
June 9β10, 2025 β Online open training session
Price:
-
750 EUR per participant
-
A 10% discount applies to the second and each additional participant from the same plant
Payment Terms:
Invoices will be issued after the service has been delivered. Payment is due within 30 days from the invoice issue date.
In-house or internal online training sessions can also be arranged for companies. For details, please contact our office.
An optional additional workshop day can be added upon client request.
Price includes:
-
Participation in the training
-
Training materials
-
Certificate of completion
-
12 months of free consulting support for participants
Check also our articleΒ 10 changes You need to know when working with Stellantis ex-FCA