A3 Report training
The A3 method, primarily used in problem-solving within Toyota plants worldwide and its supply chain facilities, allows for the proper definition, description, and effective resolution of problems in a quick and accessible manner.
As one of the essential tools in lean management-oriented organizations, it forms the basis for building a culture of quality consciousness while simultaneously focusing on delivering the highest value to the customer.
Training agenda:
1. Introduction to the training, familiarizing participants with the basic principles of problem-solving and providing a brief description of the application of the A3 method
2. Discussing the structure of the A3 report in relation to the PDCA cycle
3. Presenting the tools used in the A3 method:
-
- 5W2H
- PFD (Process Flow Diagram)
- SMART
- Ishikawa
- 5Why
- Brainstorming
- Action Plan
4. Building an A3 report from scratch, working in groups with the support of the trainer
5. Reviewing selected A3 reports and exchanging observations
6. Constructing a model A3 report for a selected case from the training
7. Summary, open question session, concluding the training
8. Optional Panel – Collaborative construction of a model A3 report for a suggested case by the group
Intended audiences:
- Internal quality
- Customer quality
- Production leaders
- Process quality
- Managers at all levels
- Production operators and supervisors
Submit a request
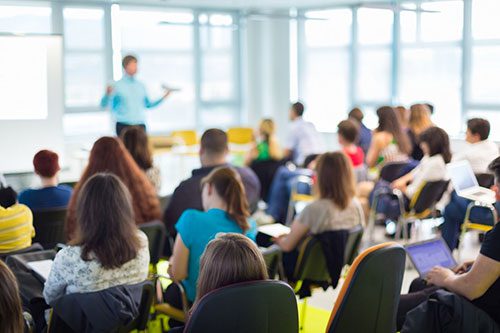
Training program
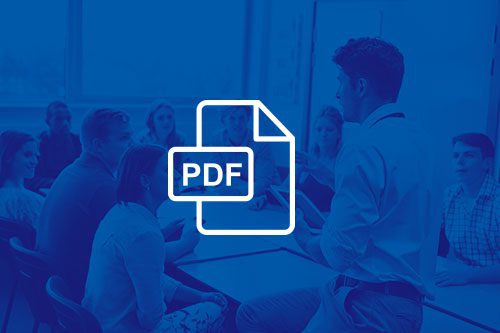
Automotive Quality Solutions
Participant will learn:
- Acquiring the necessary knowledge for effective problem-solving in the organization
- How to communicate among all team members during problem-solving
- Implementing a systematic report structure that positively influences the promotion of a Lean culture within the organization
- Increasing the effectiveness of the plant
- Enhancing the organization’s competitiveness through the application of universal methods utilized in the A3 Report, such as 5 Whys, Process flow diagram, Ishikawa, 5W2H, and SMART
Training Objective:
Familiarize the team with the A3 Report as:
- An effective method for problem-solving in all areas of the organization.
- A systematic way to report team progress following the PDCA method.
Introduce the concept of defining goals using the SMART method as an effective goal management tool.
Automotive Quality Solutions
Price:
Price:
For internal trainings, please get in touch directly with office.
Price includes:
- Training participation
- Training materials
- Certificate
- 12 months consulting for participants