Special characteristics and their appropriate management in the automotive industry are key aspects of ensuring the quality, safety, and performance of produced vehicles. Their implementation is carried out in specific steps assigned to the launch plan milestones.
Phases of Special Characteristics implementation
Identification
The first step in managing special characteristics is their identification. Here, we can apply several approaches, including product design, prototyping, and testing. The identification process should be comprehensive. The starting point is the collaboration of the engineering department with the customer (for co-design projects).
It should also take into account all the relevant features and aspects of the given project, as well as the analysis of customer needs and expectations.
Documentation
Verification and validation
We carry out these two steps to ensure that we meet the appropriate requirements and specifications in the engineering and project documentation for the defined characteristics. Here, we can choose between testing, simulation, or analysis.
The topic of simulation is very close to me, as my major in college was related to finite element analysis (FEA) used in structural analysis. However, as you can read, my passion became the automotive industry :).
Monitoring
Continuous improvement
This concept is closely related to the Deming cycle. If there are any deviations from the project requirements, we take appropriate actions.
The Design Failure Mode and Effects Analysis (DFMEA) is one of many activities conducted in the early project launch phase. If we are responsible for the project, our engineering department will conduct the DFMEA. Special characteristics play a crucial role in DFMEA because they can affect the potential failure and the severity (also known as gravity) of its consequences.
For example, if a component’s special characteristic is its ability to withstand high temperatures, it is necessary to carefully evaluate its potential failure modes related to temperature and assess their consequences.
An important step is to assign an appropriate symbol for each type of failure mode. The production facility should also include these symbols in the PFMEA documentation and Control Plan they prepare. You can find an example below:
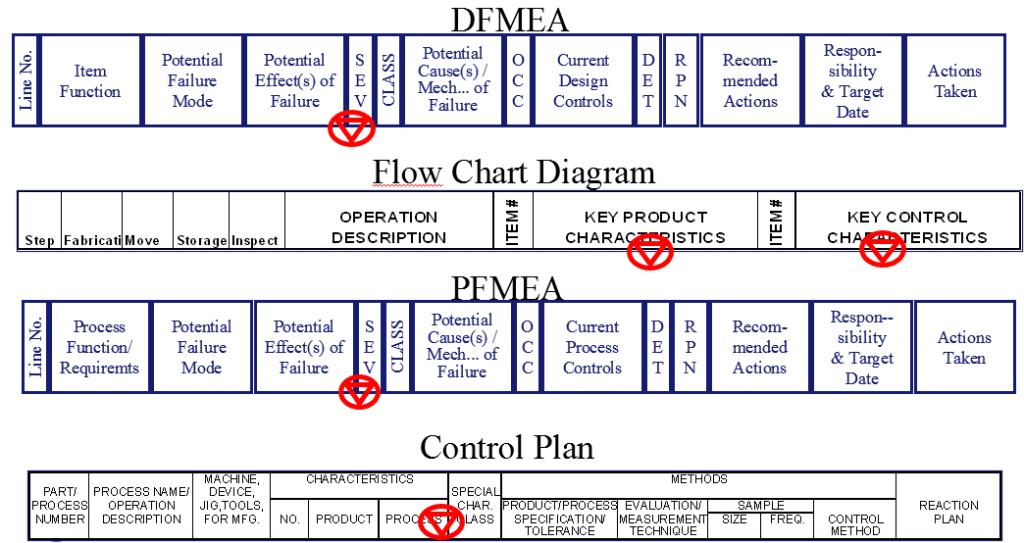
Special Characteristics – Classification
We usually divide them into two categories: Significant Characteristics (SC) and Critical Characteristics (CC).
Significant Characteristics (S.C.)
These are characteristics that are important to the customer or final client but do not have a direct impact on the safety, performance, or functionality of the product. They can still affect customer satisfaction. We should monitor and control them in the production process to ensure they meet the relevant requirements.
Critical Characteristics (C.C.)
These are special characteristics that are crucial for the safety, performance, or functionality of the product. They have a direct impact on quality, reliability, and safety, and the lack of these features can result in serious consequences. Critical characteristics require special attention and control to ensure their consistency and compliance with necessary requirements and specifications.
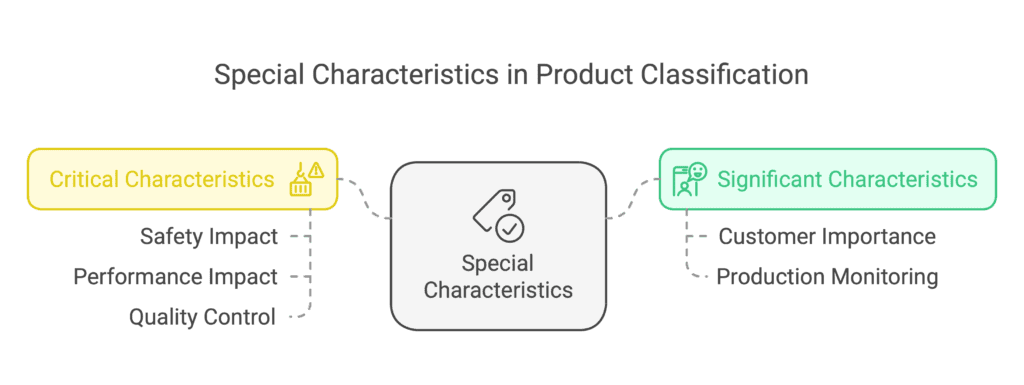
They are used to define appropriate priorities.
It is also worth mentioning the archiving of special characteristics. For the first group, the answer is simple. It is necessary to comply with customer requirements (e.g., VDA 1 manual or Customer Specific Requirements).
However, when it comes to Critical Characteristics, the storage time is additionally conditioned by:
- regulatory requirements,
- emissions,
- homologation,
- and safety.
In practice, it ranges from 15 years and upwards.
Special characteristics and SPC requirements
Requirements for Statistical Process Control (SPC) in current production usually relate to the following indicators:
- Cp – which is responsible for process spread
- Cpk – which is responsible for centering
In the case of Significant Characteristics (SC), requirements for Cp and Cpk indicators are usually lower. Why? Because the focus is on ensuring customer satisfaction and meeting their requirements and expectations. The most common requirement is for the Cp, Cpk values to be greater than or equal to 1.33.
In the case of Critical Characteristics, requirements for Cp and Cpk are more stringent. Here, the focus is on ensuring legal, regulatory, or product safety requirements. The most common requirement for the Cp, Cpk value for CC is to be greater than or equal to 1.67.
It is worth noting that specific requirements for Cp and Cpk will differ depending on the product and industry, as well as customer requirements. In cases where a special characteristic is verified at 100%, we don’t need to calculate these indicators unless the customer defines a different approach.

PFMEA in relation to Special Characteristics
Previously, when describing DFMEA, I mentioned the importance of Severity. We must remember not to modify this parameter during the creation of the production process without making prior changes to DFMEA. The organization, on the other hand, has an impact on the other parameters: Occurrence and Detection.
In the case of Significant Characteristics, Severity is usually lower because the focus is on ensuring customer satisfaction and meeting their requirements. The consequences of a potential defect may include reduced user satisfaction or increased costs, but usually do not pose a threat to safety and performance loss. In PFMEA documentation, we usually define Severity in the range of 7-8.
For Critical Characteristics, Severity is usually higher because the focus is on ensuring safety and meeting appropriate requirements. In PFMEA, we define this value in the range of 9-10.
We divide all product characteristics into three categories.
How Special Characteristics are related to IATF requirements?
When supplying components to the automotive industry, customers will almost always require us to implement the appropriate certification. In this case, we are talking about the IATF (International Automotive Task Force) standard. It specifies requirements for Quality Management Systems (QMS) for automotive suppliers, and special characteristics are one of the key elements that play a crucial role in ensuring compliance with these requirements.
For this reason, IATF requires identifying and documenting special characteristics, and implementing and appropriately monitoring a process for managing them. Among others, you can find detailed requirements in two points:
- 8.2.3.1.2 Customer-designated special characteristics
- 8.3.3.3 Special characteristics
Of course, as with archiving, individual customers may have specific additional requirements. For example, Ford manages special characteristics in the SCCAF – Special Characteristics Communication and Agreement document.
I also recommend checking the Frequently Asked Questions section on the IATF portal. Why? Because there, you will find additional guidelines related to the topic of special characteristics.
- 4.4.1.2 Product Safety. For this requirement, you will find the answer to the question of what the training levels and individual criteria are that need to be defined concerning product safety [1].
- 8.4.2.2 Statutory and regulatory requirements. Here, you will find information on whether the customer should provide the organization with detailed information regarding the intended use of the product.
Source:
1. https://www.iatfglobaloversight.org/iatf-169492016/iatf-169492016-faqs/ dated at 18.07.2024.
Dariusz Kowalczyk