The implementation of new projects in the automotive industry utilizes the Pre-launch Control Plan as one of the standard requirements set by IATF. Its main purpose is to increase quality assurance for the delivered product by enhancing controls.
Introduction
- Validate the supplier’s Control Plan applied in current production.
- Ensure the quick identification, control, and correction of any quality problems that may arise in the organization’s production plant.
It is also worth mentioning that the implementation of the Pre-Launch Control Plan is included in the IATF standard under requirement 8.5.1.1, Control Plan. In addition to this phase, this requirement typically covers series production and prototypes.
Pre-launch Control Plan in relation to Customer Specific Requirements
In addition to the IATF standard requirement, we must remember that Customer Specific Requirements have a significant impact in the automotive industry. Each OEM (Original Equipment Manufacturer) will define this document according to its own nomenclature. Below are a few examples:
- Ford: Refers to it as the Pre-Launch Control Plan. We should use it from the TT phase until final process capability approval is obtained.
- GM: Refers to it as Early Production Containment (EPC). Previously, they used the term GP12, which is no longer applicable.
- Stellantis (xPSA): Previously referred to as GP12. Currently, the procedure GSQN-004 Global Stellantis Proactive Containment Procedure introduces a new approach.
- Stellantis (xFCA): Previously referred to as the Safe Launch Plan (SQ.00009). Currently, the procedure GSQN-004 Global Stellantis Proactive Containment Procedure introduces a new approach.
As we can see, the leaders in defining additional requirements are companies that belong to the Big Three American companies (GM, Ford, Chrysler bought out by FIAT). On the other hand, the approach of German customers is more pragmatic. They assume that regardless of whether it is a pre-launch phase or ongoing production, the delivered products must be of the same quality level.
In such a situation, the organization defines the Pre-launch Control Plan according to internal procedures to meet IATF requirements.
Pre-launch Control Plan – implementation phases
When preparing to validate this document, we must consider what it will contain. It must account for all known critical aspects of the product and process, as well as the Control Plan in current production.
Additionally, the approval should not relieve the organization of its responsibility to include in the plan all characteristics that it considers relevant based on its knowledge of the production process, i.e., its know-how.
For example, the supplier of the front insulation may additionally define the measurement of the weight for the finished product, correlating it with the appropriate, acceptable level of acoustics, even though the customer’s drawing does not include such a requirement.
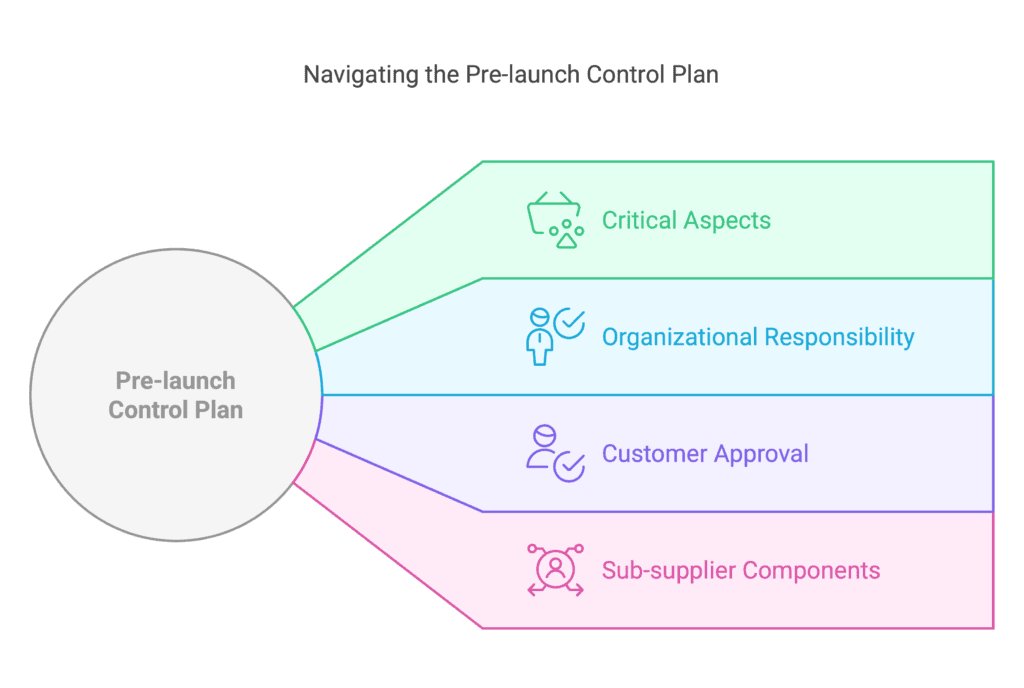
However, the company should check whether the customer’s representative needs to approve the plan, referring to the Customer Specific Requirements. We can also check whether it needs to be extended regarding components from sub-suppliers.
The standard duration for this activity begins with the production of the first parts intended for the production of pre-launch cars. Regarding the closing date, we have several strategies:
- 90 days after SOP: After the official Start of Production, when the customer’s engineering team gives the “green light” to the plant to build cars intended for sale, based on defined indicators.
- Based on the quantity of produced parts: An important strategy for supplying optional parts (e.g., low volume) such as sunroofs, automatic gearboxes, or 4×4 systems.
- Until final approval of process capability: Used by Ford, as mentioned earlier.
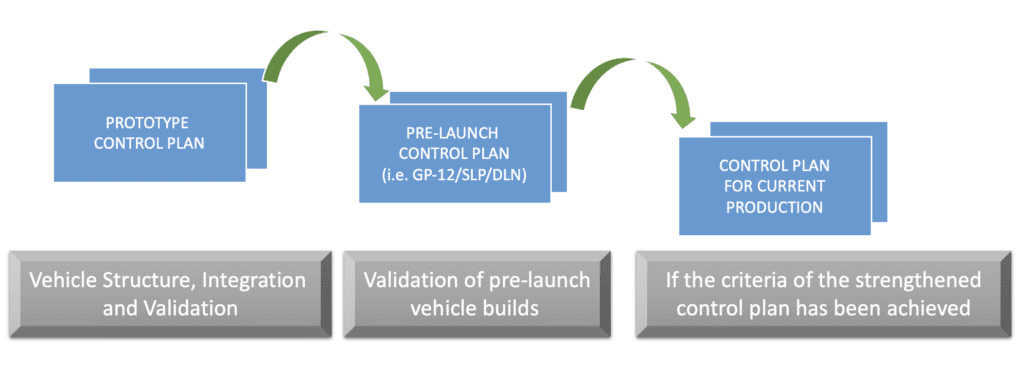
Typically, the company must also define a specific station, which should be offline, separate, and independent from the normal production process. It can also be at the end of the production line.
What are the exit criteria?
We already know how long the Pre-launch Control Plan should be valid. However, specific criteria must be met for the conclusion to occur. These include:
- No notifications from the client’s plant within the timeframe specified for the “duration.”
- If a nonconformity is found, the defined control is maintained for an extended period. Another scenario involves the quantity of parts produced after the implementation of corrective actions. This continues until the end of the period agreed upon initially. This depends on which event occurs last.
- If the customer plant finds a non-conforming part during such control, it may inform the supplier to initiate additional escalation, e.g., 3CPR ex-CSL-2/CL, etc.
Just pre-launch phase?
The Pre-launch Control Plan is not limited to this phase only. If the company significantly modifies a product during current production, it should consider launching this activity based on an internal risk assessment. The client may additionally make such a request.
The second scenario where it makes sense to restart reinforced control is during downtimes. This includes both planned summer breaks and scenarios where downtime results from a lack of customer orders for an extended period.
What else is worth remembering?
The control of pre-launch production requires the implementation of appropriate identification. Customers may require, for example, a green round sticker on finished products. Why? To distinguish that this product has undergone reinforced control compared to parts dedicated to current production.
Additional requirements may relate to the correct “writing” of the Pre-launch Control Plan. This means identifying the stations for which they carry out this control and using the appropriate colors in the document.
You can download an automatic, editable Excel form for free on the Free Quality Tools
Document name: Control Plan – Excel form
Dariusz Kowalczyk