When creating an 8D problem solving report to address internal or external quality issues, it’s important to adhere to a few fundamental principles. These principles ensure the report comprehensively covers all aspects of the problem and enables the organization to implement effective corrective actions.
The three most common challenges are:
Lack of Consideration for Risk Analysis of Service Parts Delivered to Distribution Centers
When conducting a risk analysis, it’s crucial to consider not only production parts sent to OEM car assembly plants but also service parts sent to service distribution centers. According to the updated IATF terminology, a service part is approved by the vehicle manufacturer (OEM), unlike a spare part, which lacks such approval.
Additionally, some customers (e.g., Stellantis xFCA and FORD) have specific classifications for quality complaints related to service parts.

Therefore, when developing a risk analysis for parts sent to OEMs, ensure that you address whether parts with identified quality problems have also been sent to service distribution centers. Extend Interim Containment Actions (ICA) defined in step D3 to cover these areas when applicable. Examples of such actions include sorting, material removal, and other measures.
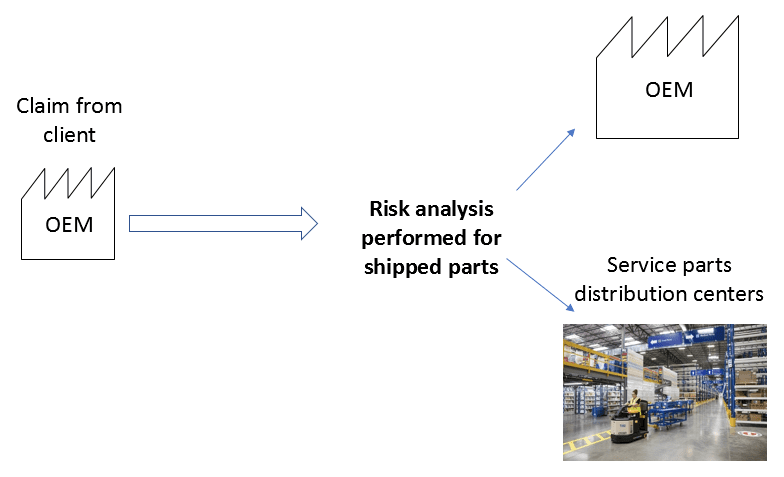
Therefore, when developing a risk analysis for parts sent to OEMs, determine whether your organization has also sent parts with identified quality problems to service distribution centers. Extend Interim Containment Actions (ICA) defined in step D3 to cover these areas when applicable. Examples of such actions include sorting, material removal, and other measures.
Actions Defined Based on Problem Symptoms Instead of Root Causes
One common pitfall occurs when teams define actions based solely on symptoms rather than identifying the root cause. For example, during root cause analysis using methodologies such as the 5 Whys, teams may fail to ask enough follow-up questions to uncover the actual root cause. As a result, the problem may remain unresolved, leading to recurrence and potential client escalation.
This scenario can have severe consequences, such as customer-mandated production process verifications by representatives (e.g., SQE or STA) or enforced 100% inspection of manufactured parts through:
- 3CPR (3rd Containment Problem Resolution) or
- CSL-1 or CSL-2 (Controlled Shipping Levels).
The only situations where symptom-based actions may be considered are:
- Quality issues related to safety, with a severity rating of 9 or 10 per FMEA guidelines.
- Problems involving a large volume of shipped parts.

In these cases, actions should align with Emergency Response Actions defined in step D0: Problem Definition.
Lack of Traceability for Subcomponents
Addressing traceability issues during 8D problem-solving is often too late. Proper traceability planning should occur during the initial APQP (Advanced Product Quality Planning) phase.
To define effective traceability, assess the risk of nonconformance associated with subcomponents and their potential impact on the final product. This evaluation should focus on severity and guide the implementation of an appropriate traceability system.
You can download an automatic, editable Excel form for free on the Free Quality Tools
Document name: 8D Report – Excel form
Author: Dariusz Kowalczyk